Cutting Edge Technology
SolarSpace is using Cutting Edge Solar Energy Generation Technology developed by world-renowned Astrophysicists and top-class Researchers and Engineers at the University of Arizona, a world leader in giant telescope optical design and manufacturing. At the University of Arizona’s Steward Observatory Mirror Laboratory, lightweight mirror designs enabled the construction of some of the largest astronomical telescope mirrors in the world, including the 6.5-meter mirror for Multiple Mirror Telescope (MMT) and the two 8.4-meter mirrors for the Large Binocular Telescope Observatory (LBTO).
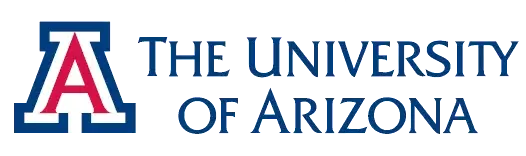
In SolarSpace technology, sunlight is focused by large mirrors and converted into electricity by small multi-junction solar cells with very high efficiency. Patented optics deliver sunlight concentrated by a factor of 1,000x to the cells, evenly divided among the cells for very high overall efficiency.
SolarSpace holds an Exclusive License from the University of Arizona (through Tech Launch Arizona) to commercialize this technology, including the mirror manufacturing method and the optics.
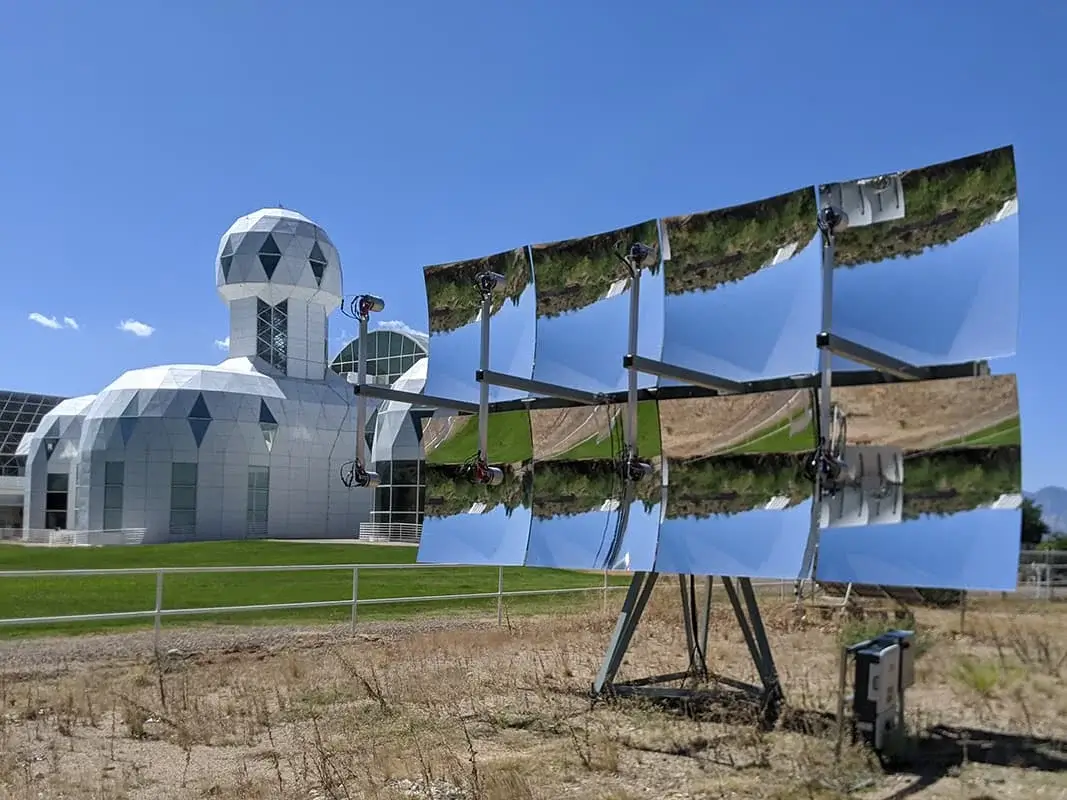
With SolarSpace's unique optical configuration, the sunlight is reflected and focused by a large, curved mirror bringing the sunlight to a focal point. At the focus, the light enters a small Power Converter Unit (PCU) through a ball lens. The concentration of the sunlight at the focal point is so powerful that it can melt a hole through a 1/4" thick steel plate in under 10 seconds.
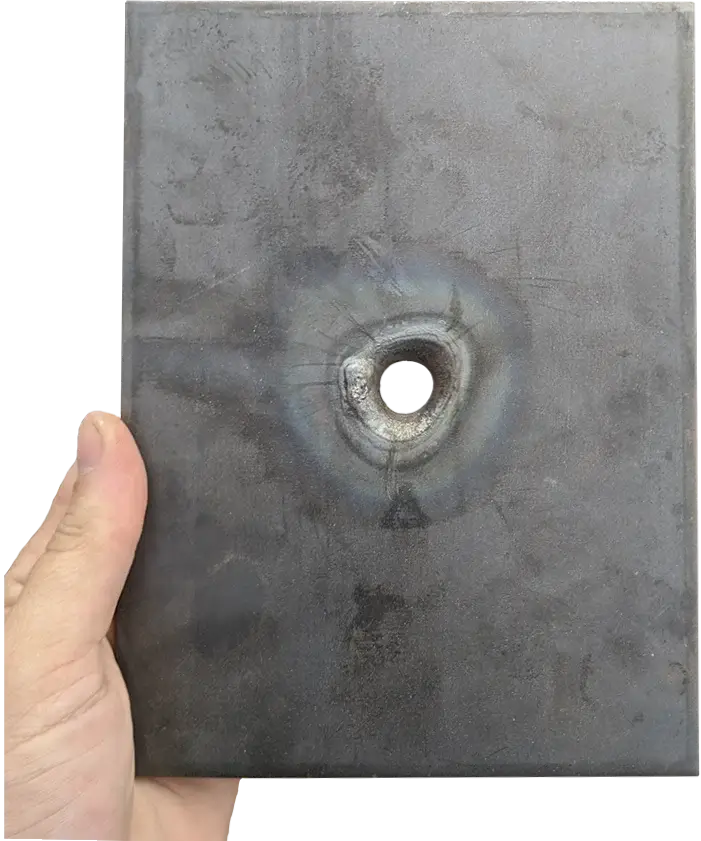
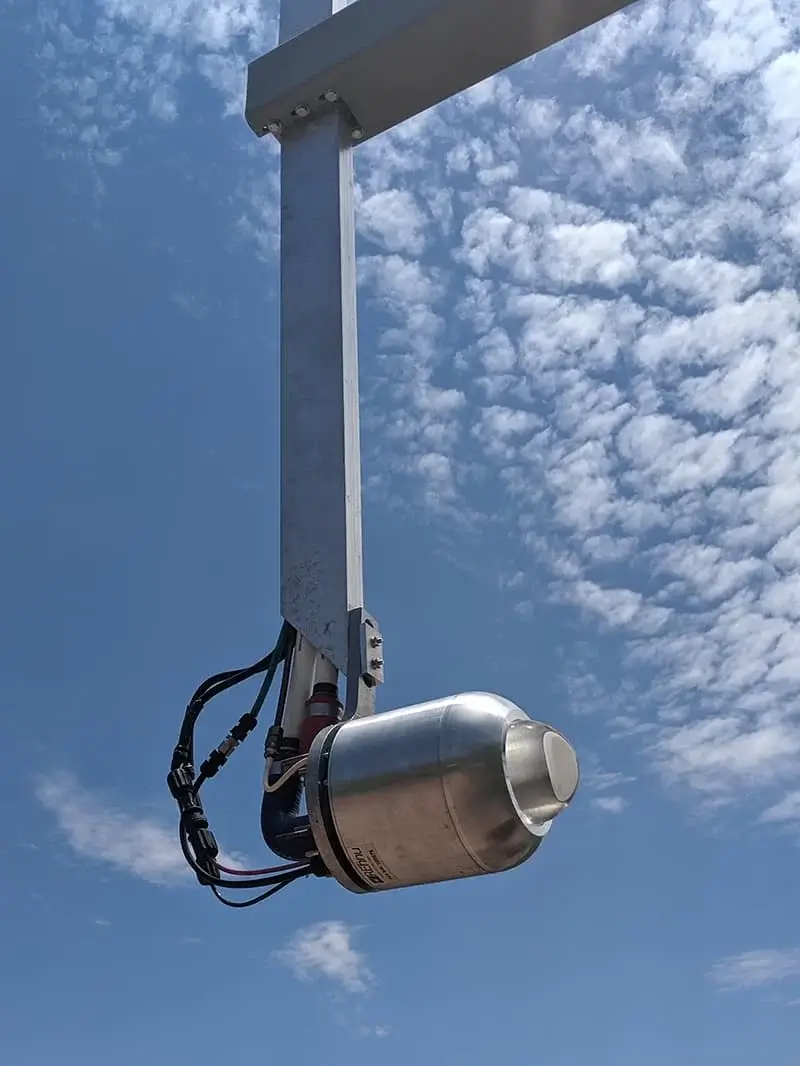
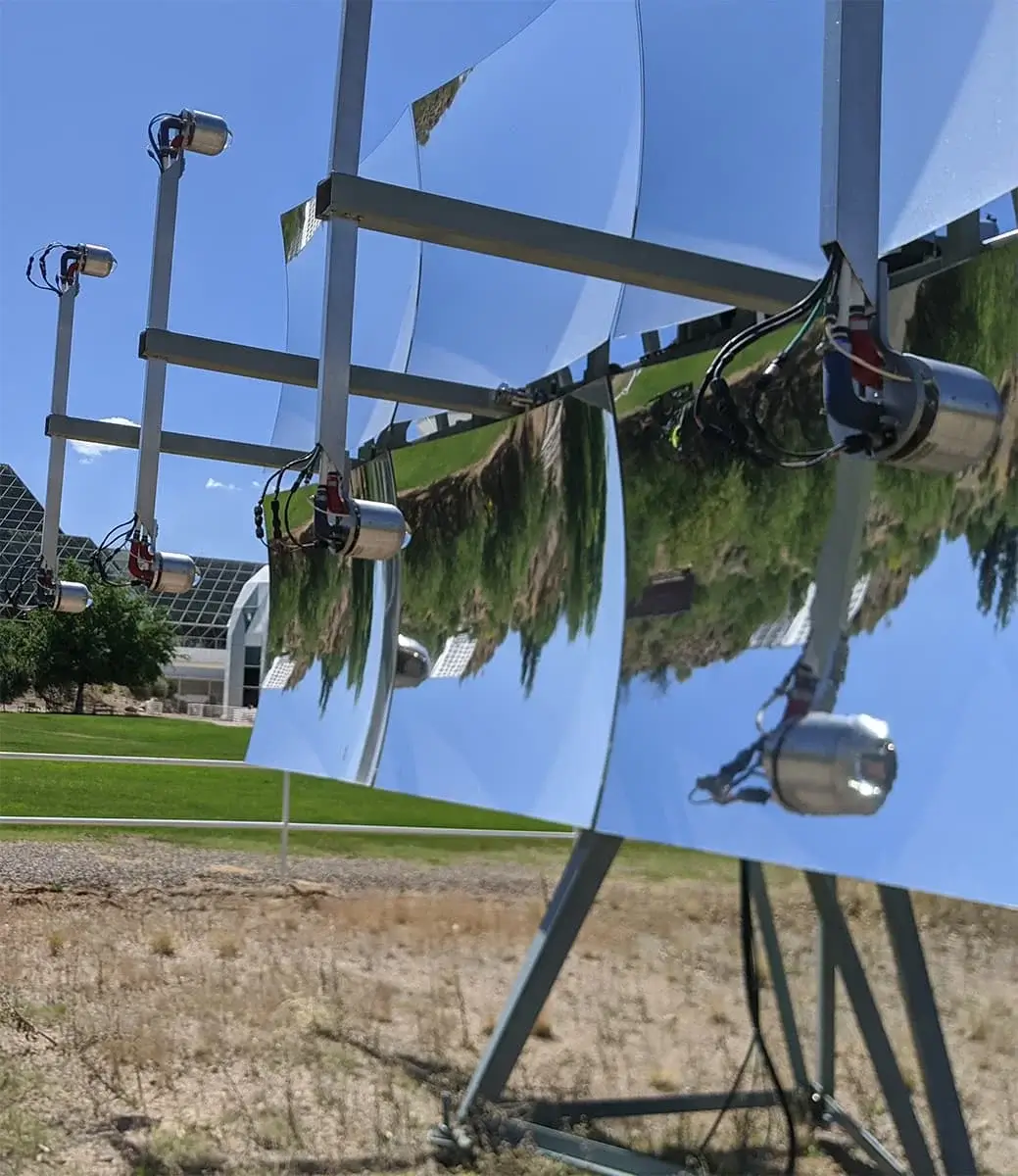
Each photovoltaic mirror module is a 30 ft2 glass mirror and 36 Multi-Junction Cells in a small Power Converter Unit (PCU). Inside the PCU is a unique origami-optics reflector which divides all light uniformly among 36 multi-junction cells, at 1,000x concentration. The cells are mounted on 4 circuit cards, nine cells to a card.
Multiple mirror modules are co-aligned on a lightweight Dual-Axis Tracker and pointed directly at the sun, maximizing total electrical output from Sunrise to Sunset.
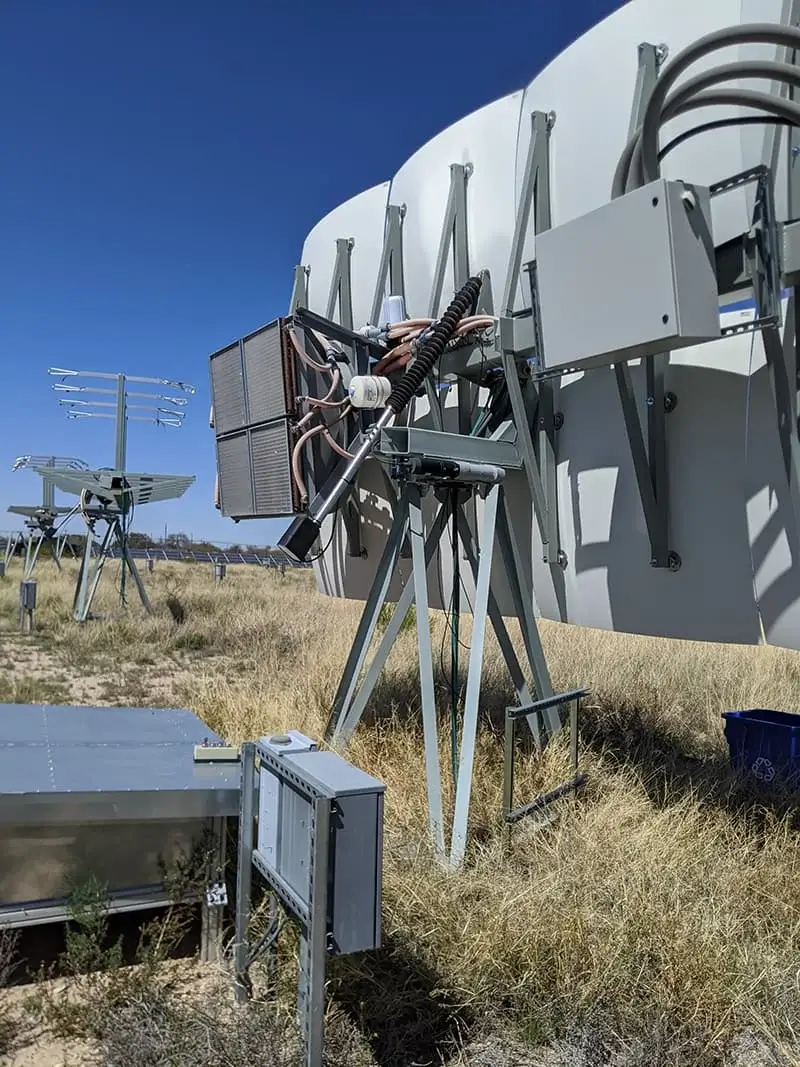
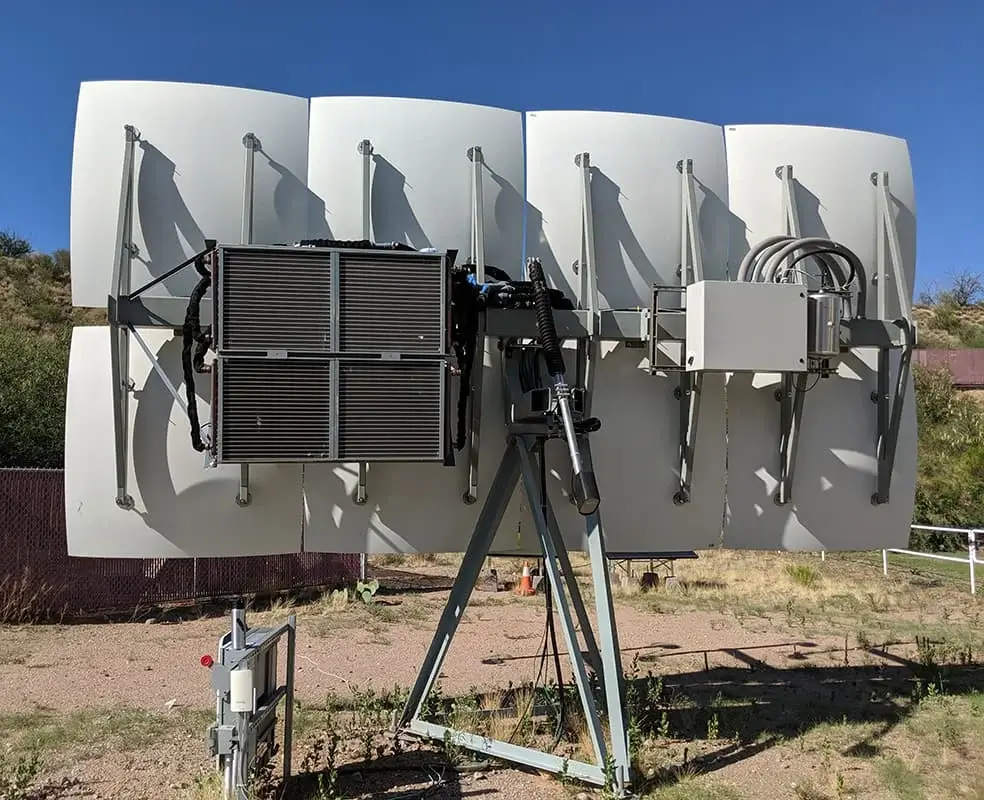
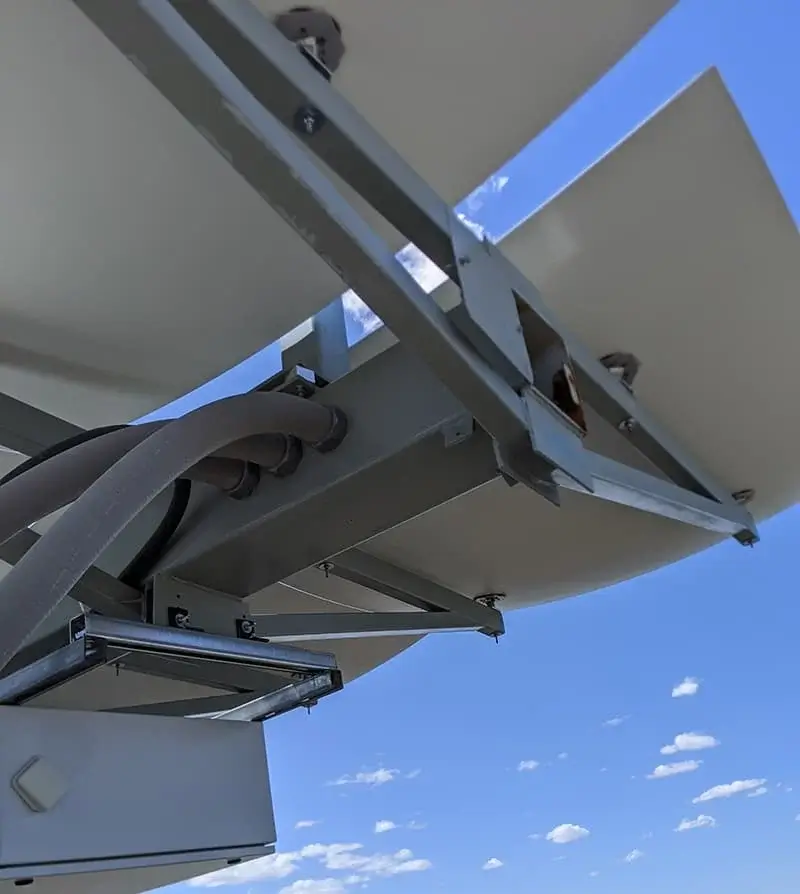
NASA Technology
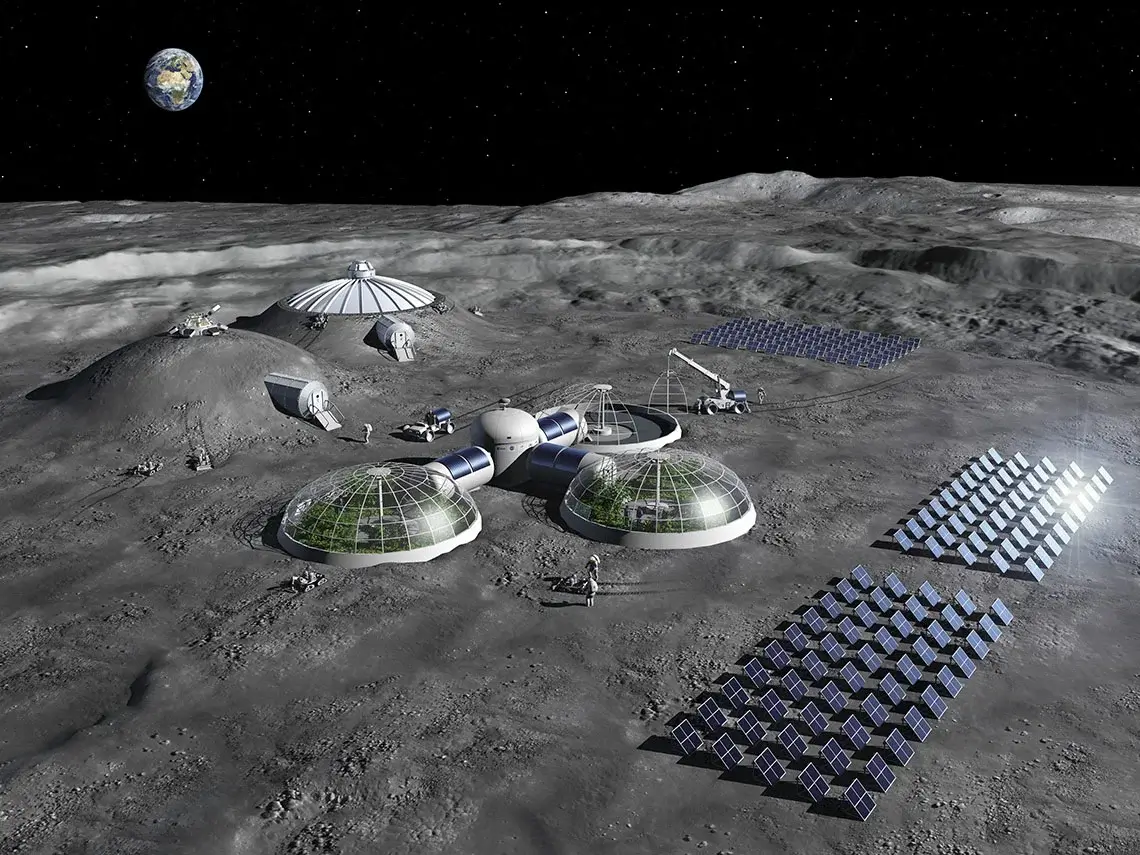
SolarSpace licensed NASA’s Thermal Recovery Energy Efficient System (TREES) and signed Space Act Agreement with NASA.
Designed for harsh environments with very little or no service, NASA Thermal Recovery Energy Efficient System (TREES) converts Heat into Sound Waves, and Sound Waves into Electric Power or Cooling with unprecedented efficiencies. The heat generated at the focal point produces a high-intensity acoustic wave, created from the temperature gradient between the hot and cold heat exchangers. This acoustic wave energy propagates through thermoacoustic power tubes, where it can be used for cooling or converted to electric power via a linear alternator. This technology has no hot moving parts, plumbing, or wiring and is therefore virtually maintenance-free.
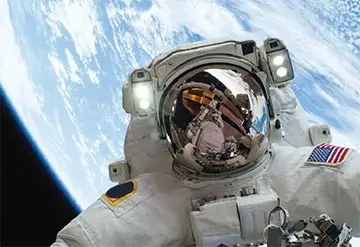
Dual-Axis Trackers
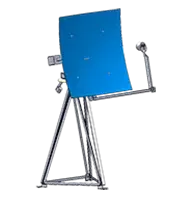
M1 Dual-Axis Tracker
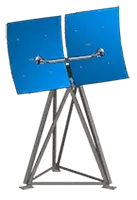
M2 Dual-Axis Tracker
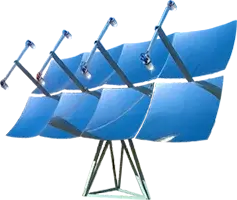
M8 Dual-Axis Tracker
SolarSpace Dual-Axis Trackers are using an array of mirrors and receivers, in landscape format. The sizes were chosen to minimize system cost based on a number of factors. The elongated landscape format minimizes self-shadowing, while the relatively small size minimizes wind load, mass and fabrication cost per unit area. It also simplifies installation and maintenance. The small size also allows low mass of steel per unit area supported.
The mirrors are axisymmetric paraboloids of 1.5 m focal length generating 1,000x concentration and the sun is tracked with 0.01° accuracy. Mirrors are square, 1.65 m on a side with area 2.7 m2, and are made from a single piece, low-iron, 4 mm thick B270 glass. The back surface is coated with silver and then over-coated with copper and paint for protection. The mirrors are supported by four aluminum pads attached by silicone adhesive. The mirrors are mounted on a conventional fishbone elevation structure with cross ribs and attachment points. The “tee” structure attached to the fishbone spine support the receivers above the mirrors. Tracking motion in elevation is driven by a linear screw actuator and in azimuth by a slewing bearing. The applied gravity and wind loads are transmitted to well-spaced ground supports. Wind forces and torques on the supported mirrors are transmitted to the ground supports as predominantly lateral or vertical forces, rather than torques. The supporting pedestal is a steel angle iron, secured to the ground by three screw anchors. These are lightweight, take only a few minutes to install with lightweight equipment, and are immediately ready for use. No concrete is used in the foundation.
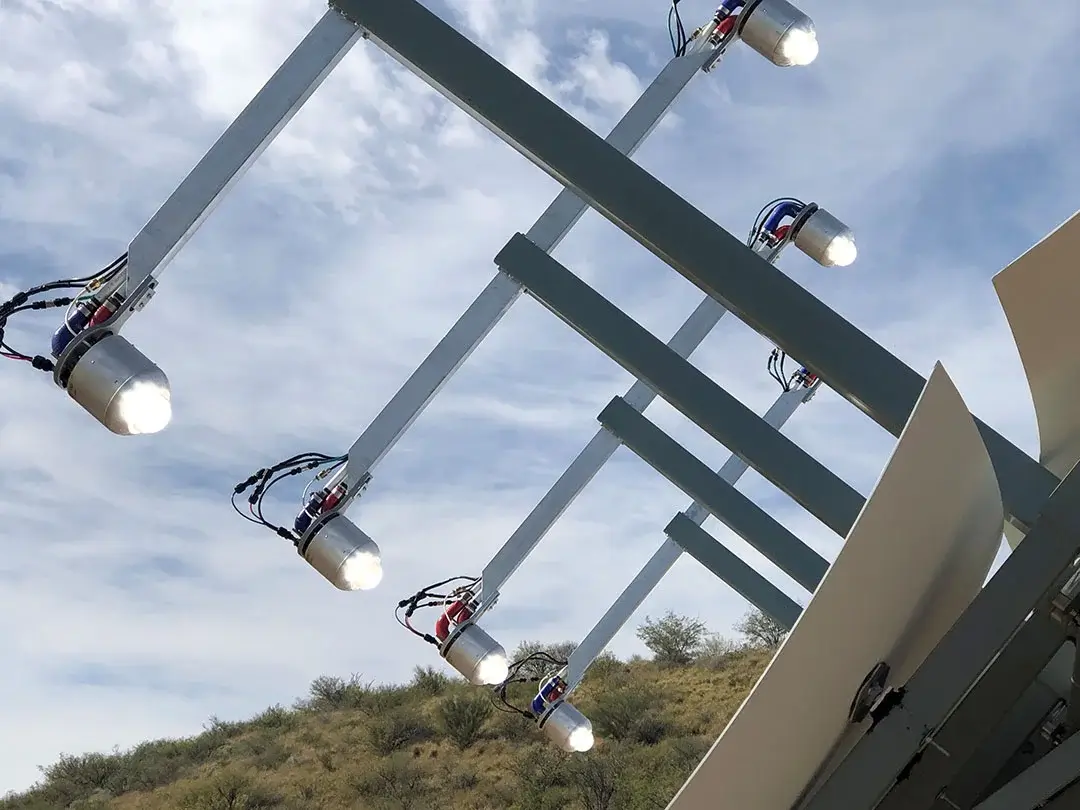
Software
Today, vast software solutions are available for managing traditional PV solar or wind farms, but there is nothing on the market that addresses more complicated and specific needs of CSP. All known CSP plants run and operate on custom designed software solutions specific to their needs with specific hardware used. It’s very difficult to integrate new or updated sensors, controllers, pumps, or other 3rd party equipment.
SolarSpace is developing an E-Management Platform (EMP) to run, manage, and optimize trackers and CSP farms. The heart and brains of the CSP Farm, with over 25,000 lines of code, it brings together all the hardware into one ecosystem and gives users full control over them with User Defined and Customized Automation Rules or Manual Control when needed. It is an All-in-One suite, incorporates various Software Algorithms, Website, Portal and an App. Our proprietary API allows seamless integration of any 3rd party IoT hardware and sensors into our platform.
SolarSpace is developing an E-Management Platform (EMP) to run, manage, and optimize trackers and CSP farms. The heart and brains of the CSP Farm, with over 25,000 lines of code, it brings together all the hardware into one ecosystem and gives users full control over them with User Defined and Customized Automation Rules or Manual Control when needed. It is an All-in-One suite, incorporates various Software Algorithms, Website, Portal and an App. Our proprietary API allows seamless integration of any 3rd party IoT hardware and sensors into our platform.
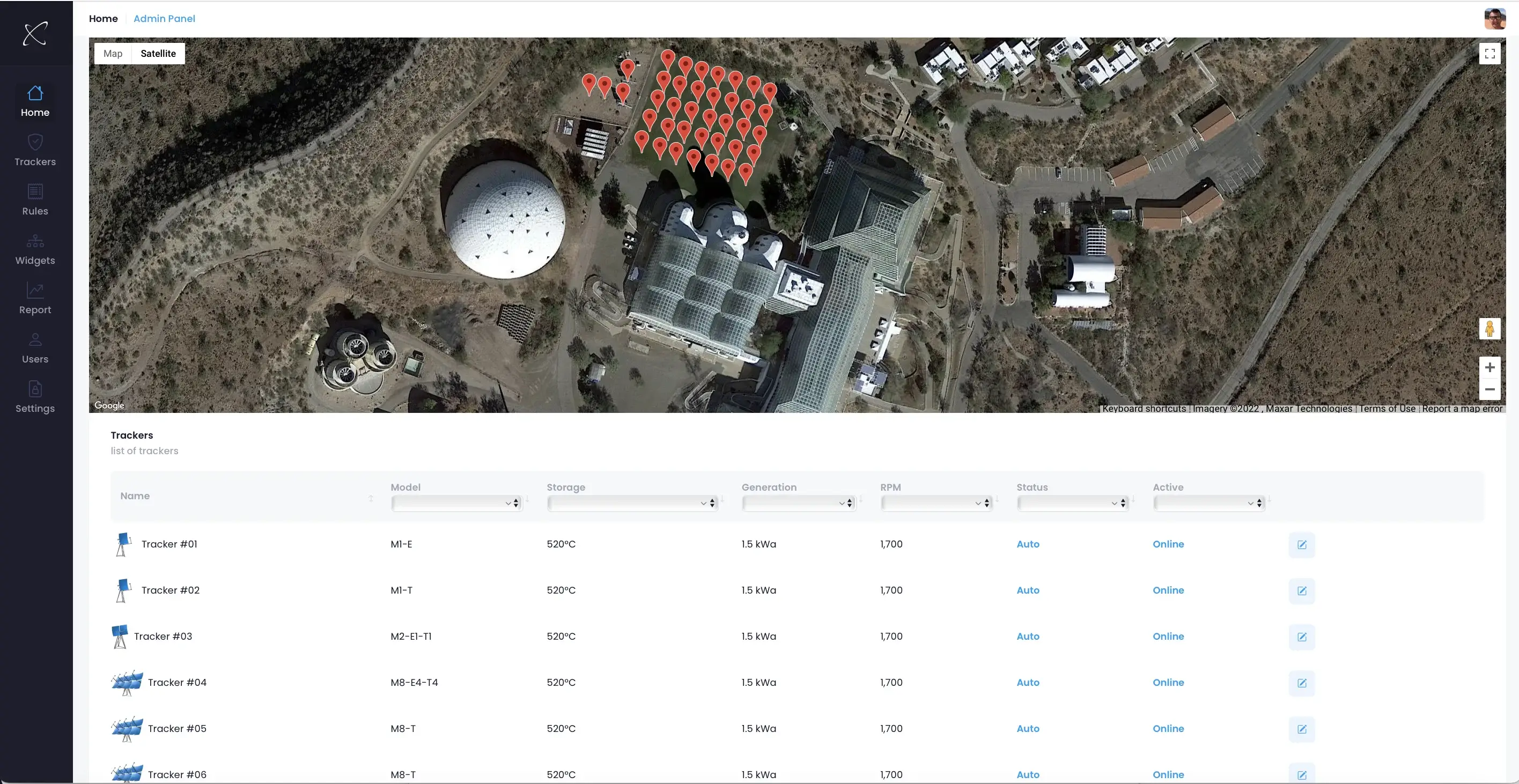
EMP is fully cloud-based platform, utilizing the latest developments in cloud infrastructure. It is written in JAVA programing language using latest Spring IOC/MVC framework, Relational Database Management System (RDBMS), and Time Series Database Management System (TSDB) capable of consuming millions of records. EMP utilizes AWS IoT Core that allows for real-time communication between stack of components. The tracker sensors and controls are built on low latency IoT specific pub/sub (MQTT) architecture.
Our proprietary Smart Tracker Command (STC) algorithm, optimizes tracker positioning and performance in real-time. It’s capable of reacting to various disastrous events, performs remediation operations, and automates disaster recovery functionality, supporting frontline communities most severely affected by climate-related disasters.
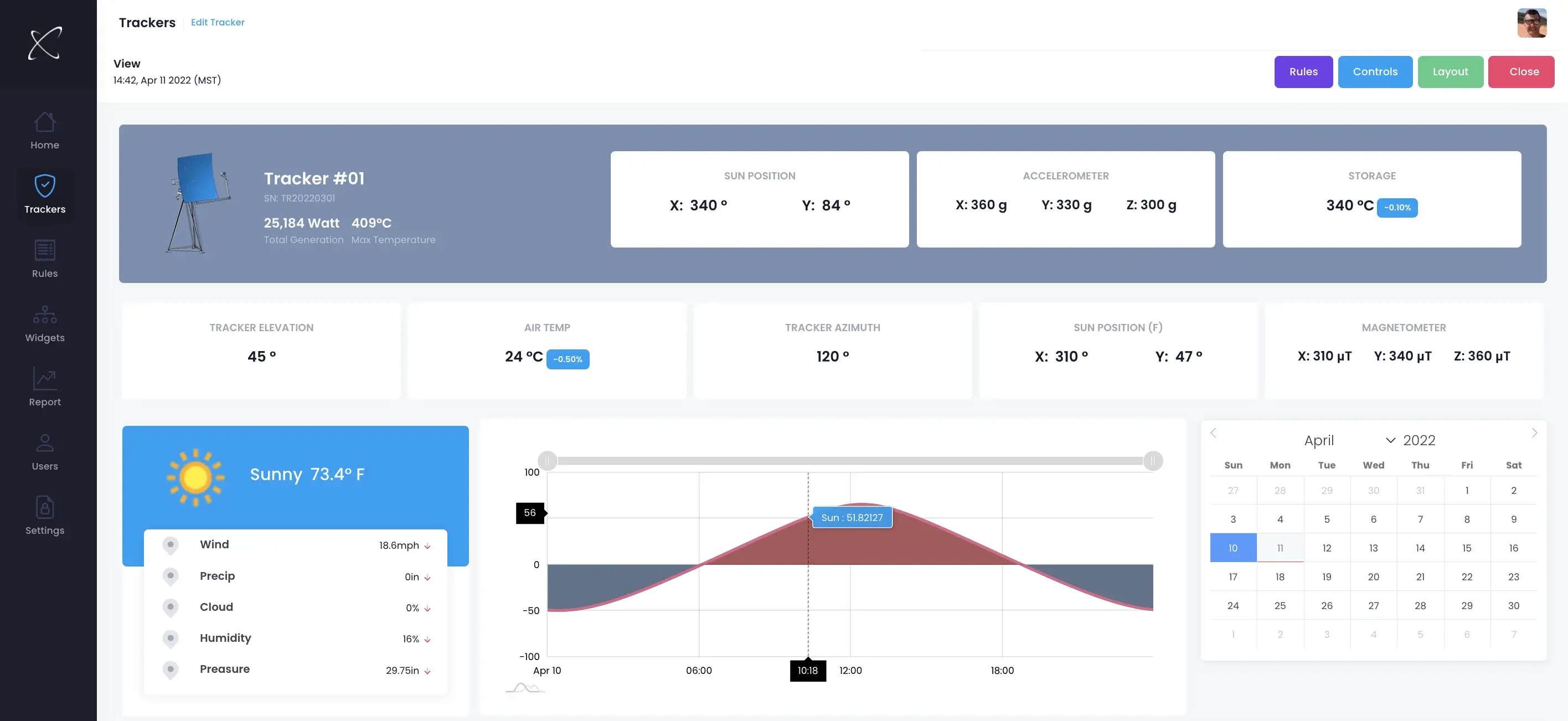
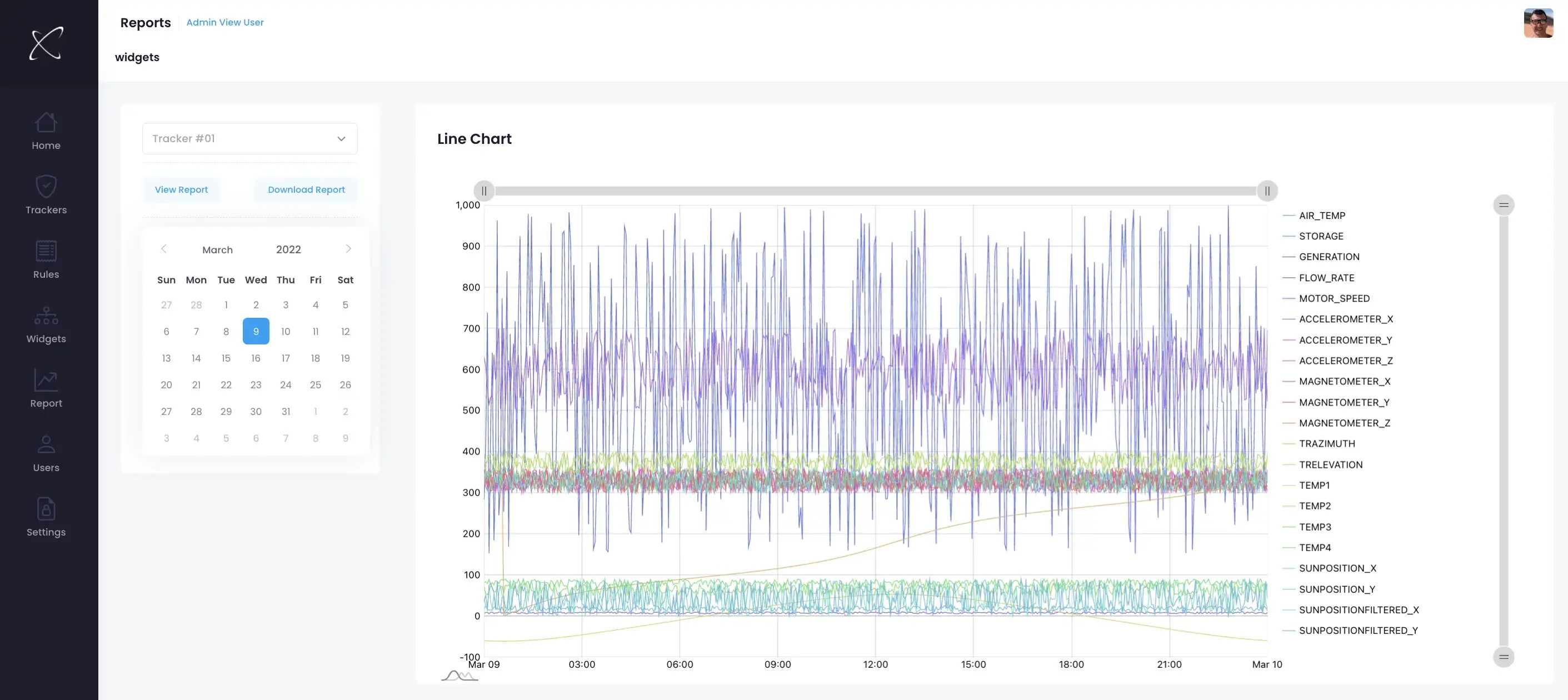
Predefined Automation Rules, Start-Up and Shut-Down Sequences, Disaster Recovery, and Business Continuity functionalities are further enhanced with ability for user-defined Custom Automation Rules. Users are able to define any scenario using “if-this then-that” logic based on any sensor readings or outside parameters (weather, time, etc).
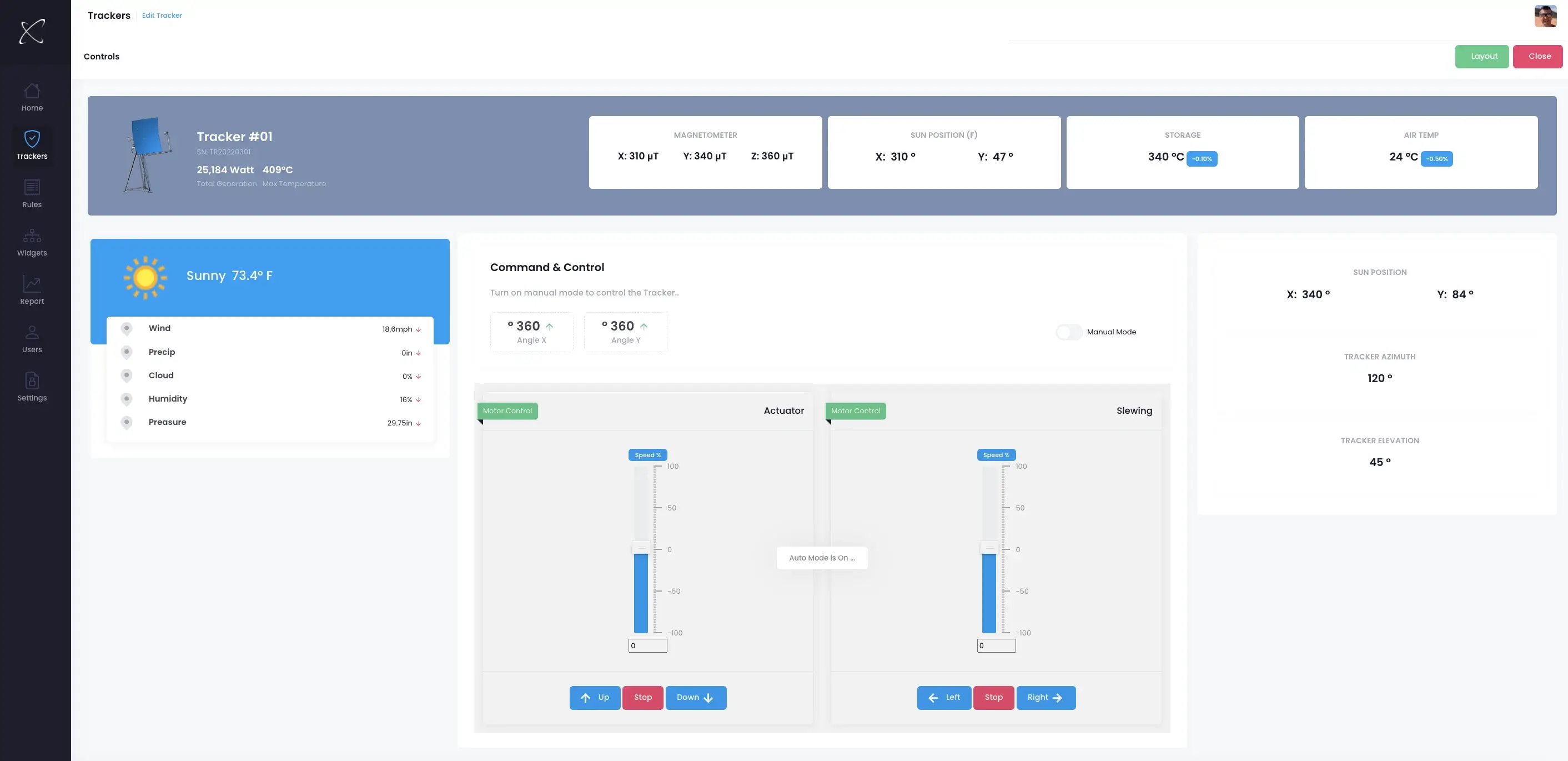
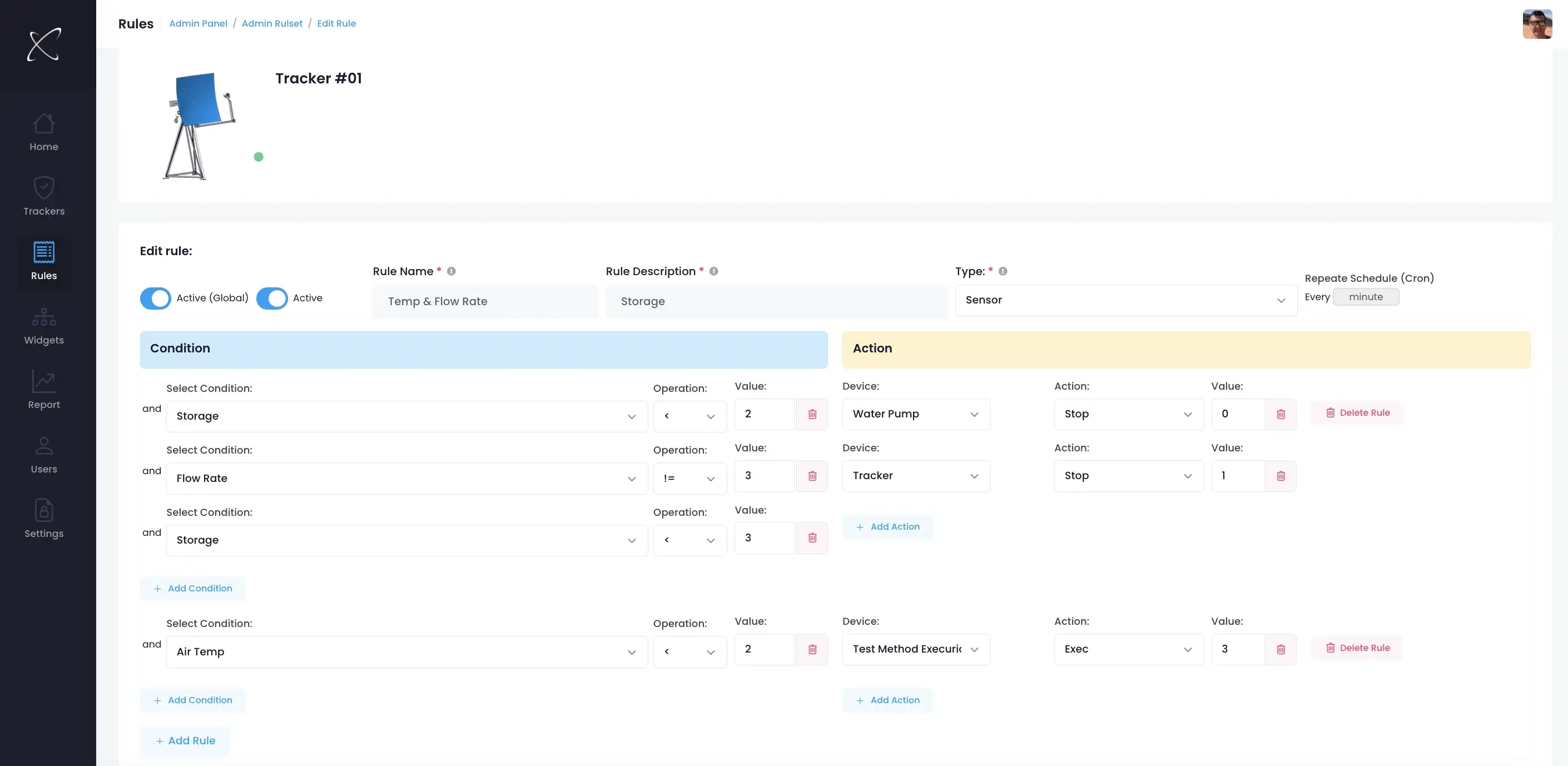
E-Management Platform will simplify integration and management of new or existing Solar Farms and CSP Plants. By design, it’s modular, extendable, and easy to integrate new or updated sensors, controllers, pumps, or other 3rd party equipment.